Unplanned downtime is a constant worry for all managers as a major shutdown would be extremely detrimental to the bottom line. A consistent goal is to have zero unplanned downtime and to prevent the possibility of losing a batch of product, or more than one batch, or shutting down a line that was not planned.
Executing a renovation project involves planning, scheduling, and front-end loading (FEL) as the initial steps. In addition, managers must also consider cost benefits of the project as well as viability or feasibility issues to ensure that time and/or funds are not wasted.
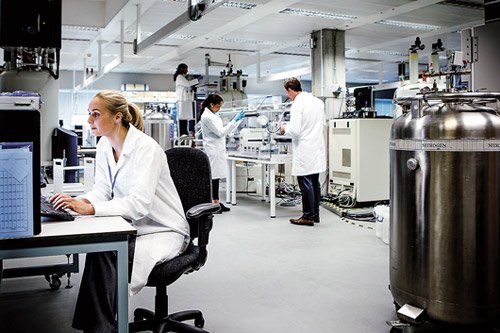
Many companies begin with the planning and capital requisitions phase, working to put the budget in place. However, some leaders only do enough engineering to set the budget, but not enough (FEL) to address risk and make decisions to commit resources to maximize the potential for success. FEL is a process that places a heavy emphasis on early planning at a disproportionate budget cost. Much of this investment is in engineering because up-front engineering consistently pays back in project savings — almost every time — and mitigates productivity and efficiency issues down the line.
In many cases, the money companies spend early on would have been spent later on in the design phase, but using it early can help to identify and create significant savings in materials and construction, which generally make up 95–97 percent of an overall project budget. Another advantage is the team that worked on the engineering process will be familiar with the project particulars and can easily transition to the design phase, thus saving time in the long term — uncovering hidden costs or feasibility issues. Plus, more engineering up front may help to prove or disprove the true feasibility of a project before a significant investment is made.
It’s all in the planning.
Sometimes it may be difficult to justify the investment needed for the higher level of planning required of the FEL process, particularly when the design budget is evaluated separately from the overall project budget. However, even these increased engineering costs are minimal compared to the changes they can help to avoid in the field or the need for an additional shutdown if the renovation project was not properly planned and phased.
Executing a renovation project involves planning, scheduling, and front-end loading (FEL) as the initial steps. Early planning provides a framework for a detailed schedule and sets boundaries for active production. Looking closely at how a facility is run and reviewing goals early on will help keep them consistent and on track throughout the project. Even experienced teams should follow the planning steps to help identify potential risks during a renovation, such as disrupting pure water flow in a high-tech environment.
During a renovation, teams must remember not to disturb the rest of the manufacturing operation. For example, it is important not to contaminate clean areas when bringing in equipment. The project must not disrupt shared utilities such as water for injection or pure water. Central systems cannot be shut down, as movement maintains the purity of the water.
It is wise to be prepared for complacent team members when trying to change a mindset or a method of doing business. Various project team members can be resistant to change or trying something new and may attempt to minimize challenges or ignore advice of team leadership. Some do not see the value of upfront engineering because they haven’t done it in the past and don’t believe the project needs it.
Having a clear, tight schedule is important to manufacturers where time-to-market is often critical. Trying to beat a competitor to market can actually backfire if manufacturers take a shortcut and skip steps; this can actually add more time to the product lifecycle.
Aim for feasibility and acceptance.
FEL helps identify the truly feasible projects and eliminate those that are not viable before time and capital is invested — or expensive manufacturing delays result from a project that isn’t viable. More planning also arms purchasers and managers with the tools they need to make informed decisions, thus boosting their confidence and competitiveness in a global marketplace.
Some leaders only do enough engineering to set the budget, but not enough (FEL) to address risk and make decisions to commit resources to maximize the potential for success. Planners can also produce a reliable scope document when FEL is done, which results in a more competitive proposal. Having a clearly outlined scope can give owners a more accurate price during the bidding phase of a design project and also provides more of an apples-to-apples comparison between bidding parties. More definition and a more competitive fee usually equate to a lower and also more reliable fee.
Consider containment safety.
In addition to considering feasibility aspects of a project, safety considerations should also be a part of the FEL early planning process. Operators must be protected from any hazardous materials, as follows:
- There must be a clean manufacturing mentality to contain potent, expensive ingredients within their containers for transport.
- Containment affects facility processes, equipment, room design, and operator access.
- Keeping handlers protected adds a layer of complexity, in addition to the normal parts of working in an active plant.
- Some manufacturing materials may have a degree of explosivity through static electricity. Special methods are used, such as grounding and bonding, to deal with a unique combination of potential issues.
- Code requirements and risks are covered in the very early planning stages of a renovation to identify potential issues; however, not all companies have expertise in this area.