When Is Bargain Commercial Real Estate a Steal?
Commercial real estate at bargain prices can seem too good to be true. Here's how to tell if you're getting a steal.
June/July 10
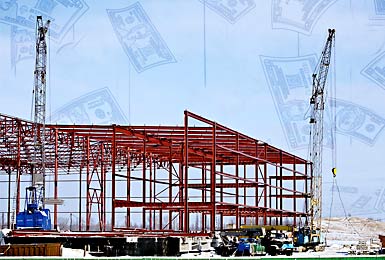
Before You Buy
Purchasing property generally requires the services of a real estate professional. Your company may retain an in-house real estate professional, or you may use a third-party broker to search for, evaluate, and complete a purchase. First, make sure your broker or in-house professional understands the intended end use of the building. As the purchaser, you must develop criteria to evaluate buildings and provide that information to your broker. End users and facility managers should weigh in on these criteria. The end users should be involved in site visits and evaluations of properties under consideration.
Similarly, your architect and engineer, in-house or out, should participate in site and building evaluation. The architect's brief space planning exercise allows you to quickly determine if sufficient square footage exists and if the building will accommodate your proposed use. Engineers should assess the building's electrical, mechanical, structural, and plumbing systems. Even if you plan to use the building for its original purpose, you need to know the condition of these systems to estimate operating and maintenance costs. And the architect and engineer should understand and compare the end user requirements to the proposed building use.
Scrutinize These Systems
Pay special attention to these building components and systems as part of the purchase evaluation:
• HVAC systems: Many industrial buildings have minimal space conditioning. Will adding new processes require more heating, cooling, and ventilation? Food, beverage, pharmaceutical, and technology processes have special cleanliness requirements. What modifications or new equipment will be needed, and is required space available?
• Structural system: Large, open bays or clear spans lend themselves to reconfigurations, but roof structures may not accommodate additional loads from new equipment. For example, a food processing company that acquired a distribution center had strict FDA requirements for heating and air conditioning. The distribution center, which had only a ventilation system, lacked a roof structure that could support heating and cooling equipment. So the company construct ed interior equipment mezzanines where new heating and cooling equipment was placed. It wasn't a difficult solution, but it incurred additional costs and had to be planned before the purchase.
• Wall systems: Industrial buildings frequently employ tilt-up construction or metal buildings with little thermal insulation. Additional insulation may be needed to meet required specifications for the proposed use. The number and placement of penetrations through building walls may be pertinent, and many buildings may have large loading docks with multiple overhead doors that may be unnecessary. Conversely, creating new openings in a wall system, particularly concrete tilt-up walls, may not be feasible or cost-effective.
• Floor systems: Industrial buildings generally have four- to six-inch-thick concrete floors. Analyze floors for structural adequacy if new equipment or changing loads are anticipated. Floor slabs may require thickening, or the building may need new equipment foundations.
• Electrical and lighting systems: New equipment or manufacturing lines could call for additional electricity if existing lighting doesn't suit the proposed use. Illumination levels may need to be adjusted, or a new lighting system may be necessary.
• Special material and hazardous substances handling: Industrial gases, fuel, hazardous chemicals, or bulk raw materials may be part of a renovated building's proposed use. They will likely require new storage, piping, or conveyance systems, and locating them can be problematic. Outdoor space, where these materials are typically stored, may be insufficient, while indoor storage may trigger stringent safety requirements.
• Truck access and loading docks: Industrial buildings usually have loading docks, but will the number and placement of truck docks be adequate or overabundant?
Project Announcements
Paragon Metal Fabricators Plans Falmouth, Kentucky, Manufacturing Operations
04/12/2025
Morris Packaging Plans Marion County, Kentucky, Production Operations
04/12/2025
Bailey Manufacturing Company Plans Laurinburg, North Carolina, Production Operations
04/11/2025
Palmetto Plastics Innovations Plans Hardeeville, South Carolina, Manufacturing Operations
04/11/2025
Meta Plans Middleton Township, Ohio, Data Center Operations
04/11/2025
CF Industries Holdings Plans Ascension Parish, Louisiana, Low-Carbon Ammonia Operations
04/11/2025
Most Read
-
Run a Job Task Analysis
Q4 2024
-
The Location Economics of Advanced Nuclear
Q1 2025
-
NEW NIMBYism: A Threat to The U.S. Economy
Q4 2024
-
39th Annual Corporate & 21st Annual Consultants Surveys: What Business Leaders and Consultants Are Saying About Site Selection
Q1 2025
-
Power, Policy, and Site Selection in 2025
Q1 2025
-
Designing Beyond the Assembly Line
Q1 2025
-
Forging Solid Foundations
Q1 2025