Energy Efficiency/Reduced Costs
In many cases, a utility upgrade may be motivated by the twin objectives of improving energy efficiency and reducing operational costs. Before effective decisions can be made, a life-cycle analysis of the business, systems, and equipment is essential. An ROI study may conclude that new technologies, such as heat-recovery systems and economizer cycles, can generate sufficient life-cycle operational savings to make the project viable, cost-effective, and sustainable.
Regulatory compliance is yet another driving force in technology upgrades. An example that applies to hazardous air emissions is MACT — the U.S. Environmental Protection Agency’s Maximum Achievable Control Technology standards. In some cases, the upgrades can be designed to achieve both energy efficiency and compliance goals.
One manufacturer replaced its aging oil, gas, and coal-fired boilers with new, natural gas-fired boilers and a condensing economizer to reduce emissions and increase energy efficiency. Although not mandated by regulation, the change from coal to natural gas reduced emissions for the plant and is in alignment with the corporation’s overall sustainability goals. The replacement of this equipment also improved the reliability and robustness of the system such that any one boiler failure would not impact facility production.
SSOE provided project management and engineering services to integrate vendor-supplied equipment into an overall solution that met the plant’s capacity needs for its current and projected future loads. Construction was sequenced around scheduled downtime. As designed, the re-installation sequence was anticipated to reduce labor costs by $170,000.
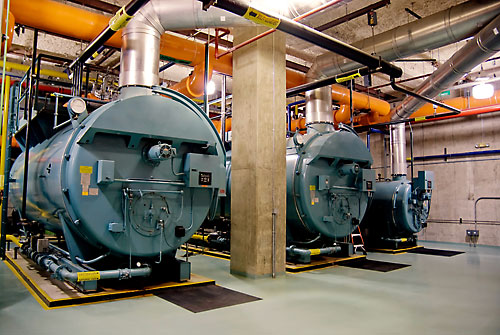
Utility expansion planning is typically driven by a business need in one or more of the following areas:
- Increasing production capacity in a successful product line
- Adding a new product
- Improving uptime
- Cleaning and asset utilization
- Increasing energy efficiency and associated operational savings
- Replacing obsolete equipment
- Improving regulatory compliance
- Meeting a corporate environmental sustainability mission
Building the Foundation for an Execution Plan
Developing the basis of an execution plan involves taking a system-wide perspective. Since a utility infrastructure expansion is both an engineering project and a business initiative, it must be based on several components:
- A clear comprehension of the business objectives;
- An evaluation that identifies each plant’s production capacity;
- An audit that assesses the capacities and condition of existing utility systems; and
- An understanding of the constraints on the proposed expansion.
The team’s evaluation of the company’s facilities identifies capabilities that may be tapped to maximize the system’s existing production and utility infrastructure. For example, it may not prove optimal to expand an existing plant because there are opportunities to shift production among other existing plants to support the business for a lower capital expenditure. However, when expansion is determined to be the most feasible alternative, a system-wide perspective enables the team to identify opportunities to offset construction-related downtime, such as building inventory at another plant.
Developing an Effective Execution Strategy
Generating an execution strategy involves assessing needs, risks, and constraints at the facility level. Therefore, the team must look at the impact of the project on production at that level. It must work closely with plant managers and key personnel from all disciplines, as well as equipment vendors and utility providers, to identify and mitigate the risks to the following parts of the business plan:
- Production capacity, uptime, market share, inventory
- Employees’ benefits and status related to furlough time, as well as employee health and safety
- Flow of people and materials
- Support facilities for shipping, lockers, and offices
- Utility service capacities and utility feeds, required ?modifications, and coordination of work orders
Total Project Delivery
Total project delivery takes a holistic, value-added approach. The architectural/engineering, construction, and construction management team serves as the expert partner in providing a comprehensive solution. A Total Project Delivery approach integrates design and construction into a cohesive team, and it uses the group’s collective talent and insight to benefit both the project and the business.
A Total Project Delivery approach integrates design and construction into a cohesive team, and it uses the group’s collective talent and insight to benefit both the project and the business. Total Project Delivery improves efficiency and productivity through all phases of design and construction through improved and earlier coordination and collaboration among designers, construction managers, project managers, project controls staff, and contractors. The benefits of Total Project Delivery include fewer revisions, fewer communication glitches, and fewer delays as the project moves forward. This delivery method also results in a compressed project schedule, and it promotes equal commitment by all entities to achieving the project’s goals.
Recently, one manufacturer added one new product line with the space and capacity to add a second line at a future date to its facility, which drove a 300,000-square-foot expansion of production, staging, and warehouse space, including a 110,000-square-foot warehouse component. The new lines had to be fitted with new equipment ranging from bulk material receiving through final palletized product. Maintaining existing production was crucial to the business’s market supply, yet the locations of incoming raw materials and shipping areas for final product were located in the required expansion space. The engineering assessment revealed that the expansion would put an additional load on the plant’s medium-voltage electrical system and further strain an already inefficient plant HVAC System.
SSOE and a local partner used Total Project Delivery to provide a comprehensive solution. The team planned and executed the project in three phases. First it modified existing incoming and outgoing shipping areas. Then it modified and added to each incoming utility. Finally, while adding the necessary square footage, it changed existing systems and added new mechanical systems to improve operating efficiency. To minimize down times, construction activities were pulled forward to allow for the movement of systems in parallel to running systems — a strategy that was only feasible due to the early collaboration of design and construction.
The power utility and project team met to determine that a service upgrade from a medium-voltage to high-voltage system promised a good payback. The solution required new substations and switchgear, and these would sub-feed the existing power system for the entire plant. This increased power stability while reducing costs. The existing HVAC system was replaced with efficient gas-fired HVAC units that use return air, saving $35,000 per year in gas usage and $53,000 per year in electricity usage. Construction was completed months before delivery of the production line equipment, which gave the facility the time it needed to be completely prepped. All systems were started up and ready to go.
Utility infrastructure expansions and upgrades are never simply engineering projects. Whether a utility project is driven by production capacity, energy efficiency, regulatory requirements, or environmental sustainability, only a business-driven approach will meet the ultimate objective, which is to add value to the business using project execution strategies while also minimizing the risks.