Advanced Manufacturing Will Drive U.S. Economic Engine
Although advanced manufacturing is ready to surge ahead, it needs 600,000 qualified workers to do so.
Summer 2012
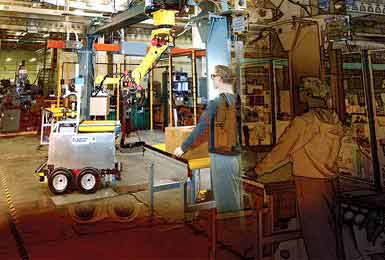
This is, essentially, advanced manufacturing - utilizing cutting-edge technology, innovative applications, and best practices to improve processes and deliver more complex and highly functional products. The increased demands for miniaturization and higher tolerances are also creating new challenges for machining and design. Key industries for advanced manufacturing are automotive, aerospace, electronics, medical devices, plastics, food and beverage, and defense/military.
Over the last several years many manufacturers have redesigned their production lines, including more process automation, to increase efficiency and reduce labor costs. As advanced manufacturing emerges from the Great Recession, the biggest challenge is not finding capital for expanding operations or upgrading equipment, or even finding more customers - it's finding skilled workers who can handle the new equipment and advanced processes on the manufacturing floor.
A recent study by the National Association of Manufacturers shows that 80 percent of manufacturers cite "finding qualified workers" as a top concern. In its 2011 "Skills Gap Report," Deloitte Consulting LLP and The Manufacturing Institute revealed that 67 percent of respondents reported a moderate to severe shortage of available, qualified workers, with 56 percent expecting the shortage to grow worse in the next three to five years. Furthermore, 5 percent of the jobs that manufacturers have open are unfilled because they can't find qualified candidates - a total of about 600,000 vacant positions.
"The hardest jobs to fill are those that have the biggest impact on performance," states Deloitte Consulting. "Shortages in skilled production jobs - machinists, operators, craft workers, distributors, technicians, and more - are taking their toll on manufacturers' ability to expand operations, drive innovation, and improve productivity."
"We have surveyed our employers and their work force issue mirrors the national picture - that even in these times of high unemployment, finding the skilled work force is a critical challenge," says Eric A. Roe, director of the Banner Center for Advanced Manufacturing in Winter Haven, Florida, a training and certification resource for Florida's advanced manufacturing work force. Roe indicates this "skills gap" in the talent pool results from the fact that low-skill jobs are leaving, mid-skill jobs are staying steady, and high-skill occupations are increasing.
"Today's manufacturing jobs definitely require higher skills competencies," he says, pointing out that the growth of high-skilled jobs in the manufacturing sector has greatly outpaced low- and mid-skill positions since 2007. "We are seeing a strong need for skilled machinists and CNC (computer numerically controlled) operators/programmers, as well as combined electromechanical or mechatronic skills for both maintenance personnel and operators."
Other skills advanced manufacturers are looking for include micromechanical systems, computer technologies and applications for drafting/ design, simulation and analysis, high-precision machining, robotics and other intelligent production systems, knowledge of composite materials, scalability, and the ability to custom-manufacture.
The Advanced Manufacturing Partnership
Recognizing the importance of advanced manufacturing in rebuilding the economy, the Obama administration created an Office of Manufacturing Policy and the $500 million "Advanced Manufacturing Partnership" (AMP), which calls for the creation of 500,000 credentialed workers in advanced manufacturing with industry certifications.
AMP will support emerging technologies that create high-quality manufacturing jobs and enhance the country's global competitiveness. The funds will be used to improve manufacturing capabilities for critical national-security industries such as aerospace and electronics, to create and test more advanced materials and technologies, and to improve the efficiency of manufacturing processes to reduce costs and speed up time to market. About $70 million will be invested in the National Robotics Initiative - a very important component to the success of any advanced manufacturing operation. (Europe and Asia have already invested heavily in robotics.)
"In manufacturing industries like aerospace and next-generation electronic systems, robotics will transform how we manufacture, not just provide incremental improvements to existing processes and production methods," says Curtis Richardson, associate technical fellow at Spirit AeroSystems in Wichita, Kansas. "In many instances robots represent a step-function shift in productivity, efficiency, and profitability that can affect every element in the manufacturing value stream, from design and analysis to sales and distribution. What's needed now is a coherent and collaborative national focus to make this possible, and the National Robotics Initiative is a great step forward."
The Georgia Institute of Technology, one of the six academic institutions that are part of the steering committee for the Advanced Manufacturing Partnership, is a leader in manufacturing robotics technology. Its Robotics and Intelligent Machines (RIM) Center will use a gift of nearly $1 million of robotics equipment from Coca-Cola Bottling Co. to create a Manufacturing Robotics Logistics Laboratory on the Georgia Tech campus. The new research space will allow RIM faculty and students to study the use of robotics in supply chain and fleet management.
"Automation has made possible a vast number of efficiencies in modern commercial logistics and manufacturing," says Henrik Christensen, director of RIM. "Using supply chains as an example, if we can use robots to optimize the entire process from start to finish, we can make improvements on a whole range of measures, such as end costs to consumers and environmental impact from transportation."
Project Announcements
Chobani Plans Rome, New York, Processing Operations
04/26/2025
NorthMark Strategies Plans Spartanburg, South Carolina, Computer Center Operations
04/24/2025
Fluid Cooling Systems Expands Burton, Michigan, Operations
04/24/2025
Fiserv Plans Overland Park, Kansas, Operations
04/22/2025
Custom Air Handling Solutions Expands Burton, Michigan, Manufacturing Operations
04/22/2025
AgriAmerica Fruit Products Expands Chautauqua County, New York, Operations
04/22/2025
Most Read
-
Run a Job Task Analysis
Q4 2024
-
The Location Economics of Advanced Nuclear
Q1 2025
-
39th Annual Corporate & 21st Annual Consultants Surveys: What Business Leaders and Consultants Are Saying About Site Selection
Q1 2025
-
NEW NIMBYism: A Threat to The U.S. Economy
Q4 2024
-
Power, Policy, and Site Selection in 2025
Q1 2025
-
Why Workforce Readiness Can’t Wait
Q1 2025
-
Designing Beyond the Assembly Line
Q1 2025