Like any manufacturing company, food and beverage manufacturers’ top concern is getting their product in the hands of consumers in an efficient, cost-effective manner. But within this manufacturing niche, it’s not simply a matter of beating competitors to the punch; in many cases, the quality and safety of the product depend on it.
After years of analyzing, building, reconfiguring, tweaking, and re-engineering, one might think that food and beverage companies have struck the perfect balance between cost-control and speed to market. However, ongoing cultural, technological, and economic changes continually push manufacturers to revisit their assumptions and decision-making processes when it comes to real estate.
Greater Flexibility Due to Intermodal
Although the qualitative and quantitative factors considered by food companies are the same as those with other site selection projects, when it comes to siting a food processing plant, how those factors are weighed and evaluated can be quite different. Companies across industries such as meats, fresh produce, beverages, candies, chemical flavorings, and nutraceuticals are likely to assign different degrees of importance to factors such as transportation, proximity to raw materials, and availability of economic incentives. Understanding what factors have the most impact on the bottom line is critical to determining where to locate the manufacturing plant.
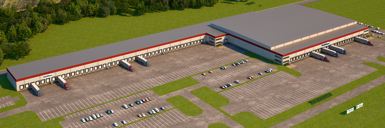
The Renaissance of Rail
For years, shipping by truck proved the most reliable and fastest means of transport for food products. And consistently low oil prices allowed manufacturers to depend on trucks without sacrificing profit. But when oil prices rise, rail transport has greater appeal. Fortunately, thanks to more sophisticated technologies, moving food and beverage by train is very different today than it was just a few decades ago.
Take, for example, the Railex refrigerated rail service that runs bi-directionally between Rotterdam, New York, and Wallula, Washington, as well as Delano, California. Refrigerated boxcars like these present produce growers and meat and dairy producers the opportunity to distribute products more cost-effectively and provide a valuable link to all U.S. destinations. While shipping via rail typically takes the same amount of time as trucking, it is at a significantly lower cost. Depending on the circumstances, a shipper could save between 5 and 25 percent by using the boxcar service versus trucking.
The market for refrigerated boxcar services has grown since the Railex launch in 2006. The RidgePort Logistics Center, a 1,500-acre industrial park 40 miles southwest of Chicago, features a unique building on the BNSF Railway specifically designed for rail-to-truck transfer. The 49,000-square-foot refrigerated facility is approximately 700 feet long, allowing for eight boxcars to be unloaded at once, and only 70 feet wide, providing a minimal transfer distance between the two modes of transportation.
For years, shipping by truck proved the most reliable and fastest means of transport for food products. And consistently low oil prices allowed manufacturers to depend on trucks without sacrificing profit. But when oil prices rise, rail transport has greater appeal. Dependence on Reliable Infrastructure
It’s one thing to make a supply chain look good on paper, but because aging transportation infrastructure is a growing concern across many regions of the U.S., ensuring primary methods of transport are reliable is crucial to a company’s success. Understanding what improvements and investments will be made over the short and long term can give decision-makers more confidence in their supply chain’s uninterrupted performance.
For some operations, such as beverage manufacturing, infrastructure like water or electric power can be a primary driver of where to locate. For example, when BrewDog, one of the fastest-growing craft beer brands in the country, was looking for a new facility, Ohio-based Buckeye Power Inc.’s ability to provide adequate supplies of high-quality water helped the state secure a new 100,000-square-foot brewery that could ultimately expand to 300,000 square feet.
Adapting to Environmental Sensitivities
It is estimated that the average American meal travels about 1,500 miles to get from farm to plate. The amount of fossil fuels used daily in transporting food and beverage worldwide is practically incalculable, and the resulting carbon dioxide emissions have a negative effect on air quality. Companies are assuming more responsibility for sustainable business practices, if not because they are positive corporate citizens, then because they are feeling the pressure from consumers who are factoring in this variable when making purchasing decisions. The fact is, consumers want to support companies that share similar values, and if a food manufacturer can demonstrate effort at reducing its negative environmental impact, it will fare well among a growing percentage of the population.
When examining the supply chain, the greatest impact on the environment comes from distance traveled. But the form of transportation is also an important factor. One boxcar holds the same volume as four trucks, making it four times more fuel-efficient. Airfreight generates 50 times more carbon dioxide than shipping by sea. Of course, the lengthy transport times needed for sea shipping aren’t feasible for many operations.
Consumers also are becoming more averse to food additives. When produce is transported long distances, it is often picked while still unripe. Gasses may be used to ripen the food during or after transport, or the food is highly processed with preservatives to keep it suitable for sale. Health-conscious consumers who have knowledge of such practices may shy away from these products, no matter how inexpensive or accessible they may be.
The Immigration Question
Ever present with a discussion of agriculture and food processing is a consideration of U.S. immigration policies and how those may change over the coming years. The availability — or lack of — seasonal labor could have a tremendous impact on the very first step of the food manufacturing supply chain. Companies heavily dependent on fresh fruits and vegetables harvested by an immigrant population are engaging labor analytics specialists to construct a picture of the labor pool today — and what it might look like five or 10 years down the road — when making decisions about where to locate a new facility or how to structure transportation contracts.
Communication Enhancements
The importance of flexibility in the supply chain cannot be overestimated, and improved means of communication have been a major contributor to more flexible operations. Modern warehousing that can accommodate advanced shipping notification (ASN) and system-directed replenishment has tightened up the supply chain considerably. Dock doors can be used with highest efficiency and food product can get to its destination more quickly. For perishables, cross-docking is more easily achieved with ASN, saving the manufacturer time and money.
Effective vendor compliance programs go hand in hand with ASN. Suppliers reduce waste by implementing best practices to ensure food product is configured for minimal damage and easy handling. The most effective compliance programs are those developed via collaboration between manufacturer, supplier, and warehouse or distribution center. More and more frequently, manufacturers are employing full-time vendor compliance managers to oversee this element of the supply chain.
Companies that hire experts to examine their supply-chain operations are able to identify inefficiencies. Often, cost-saving improvements can be made with little or no financial investment. For example, a study that counts how many times a product is touched or moved from the start to the end of a company’s supply chain may highlight processes that are compromising product freshness. Or engaging in a cost-benefit analysis may yield surprising results if it has been some time since a company has examined different transportation options. Ultimately, it is inevitable that technology, consumer preferences, economic conditions, and other variables will change over time. What is most important is that food manufacturers periodically re-examine both internal processes and the impact of external variables on operations to ensure optimal results.