Modular Construction Projects Cut Costs and Timelines
Early commitment from buyers and all stakeholders is imperative to a successful modular construction project, which can deliver on cost savings and shorten timelines.
Q3 2018
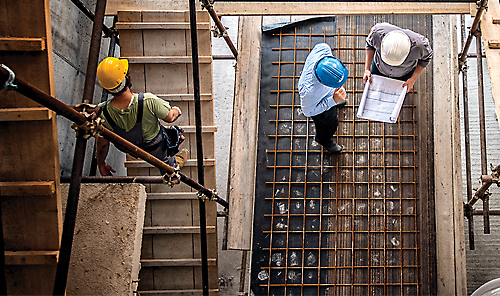
Modular design, or modularization, is a design approach that subdivides a building into smaller parts, modules, or skids, which can be independently created and then combined with different systems to drive multiple functionalities. Modular construction allows parts to be assembled at another location and then brought to the final site for finishing.
Increasingly, more companies are embracing modularization and standardization as cost savings are a major draw. Standardized design reduces costs to install and commission when all controls, electrical, and sanitation systems are of a standard design and pre-packaged. In addition, facilities use a smaller footprint since they build the same modules repeatedly, which allows for specification, thus improving quality.
With modularization, the decision to install capital can be delayed to when market demand is anticipated. For example, the first rollout may take longer as managers consider market factors, pricing, and volume demand. They tend to make more conservative estimates in an initial modularization project when they are unsure about how costs will play out. However, with subsequent rollouts, overall costs will likely be lower as companies gain efficiencies, and, consequently, the project timeline will be shorter.
Labor and Safety
The gains on modularity increase as the work sites become more remote. Shipping into distant locations and bringing in skilled labor can be challenging for any organization. For some large projects, work crews can be commissioned for a year or more. Site-labor costs can be significantly reduced with proper early planning during modularization. Pre-planning will also allow managers to keep a tight estimate on capital costs.
A strong technical leader from an experienced team will work with clients’ staff to get detail decisions made quickly and efficiently. The technology might not be new, but it’s the optimization of the delivery that makes the difference.
A recent paper plant project with a standardized design has incorporated modular construction into its regular production flow. All high elevation work — above a certain story level — is done in a controlled yard environment, which reduces the likelihood of accidents. Heavy equipment, such as steel erection and mobile cranes, can be particularly dangerous, especially with numerous people moving around a site.
The plant’s design/build cycle was condensed due to market demands. It was losing too much time in unique site construction and needed to move to a standard design to prevent lost opportunities. The facility moved to a standardized design and has optimized for modular construction, incorporating it into the regular flow.
Modular design, or modularization, is a design approach that subdivides a building into smaller parts, modules, or skids, which can be independently created and then combined with different systems to drive multiple functionalities. Advanced Work Packaging (AWP)
To significantly optimize the efficiency of site-labor costs as well as the project schedule, project leaders can also consider Advanced Work Packaging (AWP). AWP is very similar to LEAN project delivery, and is the term used on the process aspect of projects. The challenge with AWP today is with the contracting strategy. Depending on how the contracting strategy is set up, AWP allows for easier flow of information. (In a perfect world, all professionals would share information openly, yet contracts in the industry don’t always support that type of collaboration.)
With AWP and the right contracts in place, this approach allows project leaders to streamline the decisions that need to be made to release work, thereby limiting waste. In this way AWP aligns with LEAN project delivery.
To optimize AWP, project leaders seek to understand how the work is being done, and how it needs to be done to avoid helping one group and hurting another. This means all disciplines and subs need be involved and collaborating to do this successfully.
Understanding the role of technology, project teams can plan work packages, but much of the coordination depends not only on different software for different disciplines, but also how information is transferred back and forth. Therefore, a key challenge that needs to be address for AWP to be effective is upfront planning on how data will be exchanged as packages are created.
Standards and Modules
Standardization is the process of setting generally uniform characteristics for a particular design. It works in tandem with modularization, producing high volumes at low manufacturing costs. Also, standardization allows managers to be more open-minded, moving beyond the reason of “because it’s always done this way,” to exploring more efficient design and construction processes and ideas.
During modularization, standard construction is started with the largest portion possible. Modules themselves can be extremely large — almost 600 tons or the size of a football field. If the site is near water or adjacent to a dock, large modules can be transported by ship. Smaller modules are moved by rail or truck.
Once modules are in place, anchoring and pipe fitting occurs and utilities are connected. Standard modules make this process smooth since components fit together easily. The larger the module, the fewer pipe breaks and connections of equipment between two modules.
It’s All in the Planning
One of the most challenging aspects of modularization is gathering enough information and including the level of detail necessary before work can start. Project leaders must know their process design, agree on standards, and decide at what level modularization should occur. Some companies are enthusiastic about the possibility of modularization because they never considered something other than design, bid, build before. They are excited to try something unique and different.
Site-labor costs can be significantly reduced with proper early planning during modularization. Early commitment from buyers and all stakeholders is imperative to a successful modular construction project. In many cases, initial ideas and process flow diagrams are formed, but the decision to modularize is made too far into the planning stage and, consequently, the project fails.
It is important to have a good relationship among the entire project team and understand their efficiencies, how they are set up, and their capabilities for moving materials in and finished projects out. Since the planning stage can be long, many feel that it is unproductive. However, the project team can use the time to think proactively instead of falling into the reactive mode. The team can manage some aspects of the job that are not time-critical but are important from a larger perspective.
Inevitably, design variability is almost always a factor in every project, but particularly in those that are larger in scope and more time-consuming. If a project manager, for example, is suddenly replaced after a two-year time span, the details and design will most likely be altered slightly. Sound planning proactively minimizes such changes.
Global Benefits
Global companies also can reap the benefits of modularization as processes can be implemented anywhere in the world. Historically, organizations looking to expand overseas must deal with many complex transitions. However, turning to modular execution will help simplify processes in any country and make all jobs easier and much more efficient in the long term.
Project Announcements
KBR Expands Davis County, Utah, Operations
04/15/2025
TL+CO Business Solutions Plans Seabrook, South Carolina, Production Operations
04/12/2025
Paragon Metal Fabricators Plans Falmouth, Kentucky, Manufacturing Operations
04/12/2025
Morris Packaging Plans Marion County, Kentucky, Production Operations
04/12/2025
Bailey Manufacturing Company Plans Laurinburg, North Carolina, Production Operations
04/11/2025
Palmetto Plastics Innovations Plans Hardeeville, South Carolina, Manufacturing Operations
04/11/2025
Most Read
-
Run a Job Task Analysis
Q4 2024
-
The Location Economics of Advanced Nuclear
Q1 2025
-
39th Annual Corporate & 21st Annual Consultants Surveys: What Business Leaders and Consultants Are Saying About Site Selection
Q1 2025
-
NEW NIMBYism: A Threat to The U.S. Economy
Q4 2024
-
Power, Policy, and Site Selection in 2025
Q1 2025
-
Designing Beyond the Assembly Line
Q1 2025
-
Why Workforce Readiness Can’t Wait
Q1 2025