But while U.S. manufacturing is experiencing a renaissance of sorts, employers are facing a new challenge — a shortage of qualified job applicants. According to The Manufacturing Institute, roughly 600,000 domestic jobs in manufacturing remain unfilled due to a lack of qualified applicants. The Great Recession ended more than five years ago, but many Americans are still unemployed because they lack necessary skills. As a result, vital manufacturing positions sit vacant.
This is not news for those who work in economic development, regardless of the region of America they call home. Anyone who has tried to place a 21st century plant in a state or county is aware of the misalignment that currently exists between the competencies required by industry and the skills of current job applicants.
Technology and the economy change more quickly than education systems, particularly today, which means education and labor market institutions are perpetually out of sync.
In a recent survey, nearly 80 percent of U.S. manufacturers reported a “moderate” or “severe” shortage of qualified applicants, and these shortages exist in every state and every sector of the manufacturing community, according to The Manufacturing Institute. For the fifth year in a row, the most difficult positions to fill both nationally and globally are in skilled trades.
As you well know, modern manufacturing requires a new skill set, one that is more technical and flexible than in the past. It’s not enough for today’s workers to be proficient in math and science. They must also be able to adapt to an ever-changing digital landscape — one with new technologies, applications, and computer programs. This skills gap threatens not only the long-term viability of U.S. manufacturing but also the U.S. economy itself.
NAM Steps Up to the Plate
The National Association of Manufacturers (NAM) recognizes that this gap is a pervasive issue nationally and must be addressed with lasting commitment. As a member of NAM’s board of directors, I can say we take it as our responsibility to make sure manufacturers have the talent to fill today’s — and tomorrow’s — jobs.
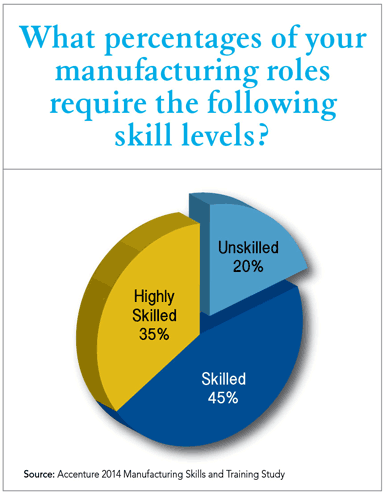
I served on the task force with 16 other NAM board members, representing both large and small manufacturers. Our charge was to find ways to bring manufacturers together to improve workforce outcomes, looking at not only the skills gap but also the implications of an aging skilled workforce that is retiring and leaving manufacturing faster than it can be replaced.
We met for nine months. We held hearing-style discussions to identify common problems across industries and explore solutions, experiences, and best practices. We met with economic development experts and think tanks, as well as local, state, and national leaders, from educators to members of Congress. The effort was completed in the fall with very good results.
We realize now, more clearly than ever, that we must align education, economic development, workforce, and business agendas to develop the talent necessary for success in a global economy. Unfortunately, our current education system appears almost completely disconnected from the economy at large.
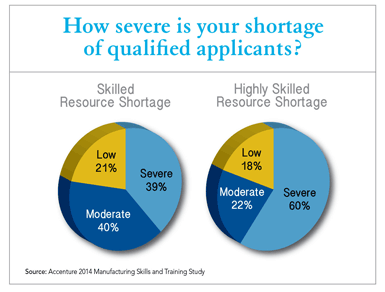
Technology and the economy change more quickly than education systems, particularly today, which means education and labor market institutions are perpetually out of sync. Not so long ago, it was assumed manufacturing would grow overseas because of cheaper labor. As a result, we are still recovering from the effects of an education era that pushed career-oriented or technical curriculum into the non-credit side of academia, sending a message to students and parents about the value colleges place on such programs.
These non-credit courses were defined as “job training” or “career” and “technical” education and weren’t considered substantive education by most students, parents, and even school administrators. A wall was built between skills training and education by institutions on both sides of that divide. Yet, these are the very skills that will lead to a job or career that actually exists.
Federal policymakers took a crucial first step toward resolving this issue last summer when Congress passed the Workforce Innovation and Opportunity Act, which will enable job seekers to access employment, education, training, and support services needed to succeed in the labor market. It will also match employers with the type of skilled workers they need to compete globally, while streamlining existing workforce development programs.
While only one in four jobs in 1970 required more than a high school education, the task force found that approximately 70 percent of today’s jobs require not only a high school diploma but also skills-based training. Employers are increasingly requiring workers to have advanced training in science, technology, engineering, and mathematics (STEM) areas. Additionally, all workers — even those in entry-level positions — must have “soft” skills considered necessary for productivity, such as a teamwork mentality and conflict management skills.
The productivity, talent, and innovation of the men and women who make up the manufacturing workforce have fueled the American economy for decades. Our workforce has been, and should remain, our competitive advantage.
Turning Discussions Into Solutions
A key discovery for us was that the most successful workforce initiatives, thus far, have been led by manufacturers who have aligned themselves to speak with a unified voice. These alliances have enabled industry leaders to set aside natural competitive tendencies to address this common need. They have been able to speak out about workforce challenges, assess common skill deficits, and create a plan for their region. Essentially, they have turned discussions into solutions.
Using these real-world success stories, the task force developed a toolkit and a step-by-step guide to help manufacturing leadership effect change at the grassroots level. These materials provide specific steps and best practices for establishing a manufacturer-led workforce development program.
The first step is for individual manufacturers to identify their own skills gaps and long-term hiring needs. Manufacturers then must collaborate within their local communities to identify the key competencies needed for new hires to succeed in today’s advanced manufacturing operations. Manufacturers carry significant weight in local communities, and speaking with a unified voice regarding workforce needs is essential to engaging and aligning key stakeholders — community leaders, educational institutions, and local and state officials — to develop a plan for local workforce training. And finally, the toolkit helps manufacturing grow a pipeline to ensure a sustainable supply of skilled talent.
Building the pipeline will require engagement with secondary school and community college educators to, in essence, reform education. NAM has already created a breakthrough skill certification system that is nationally portable and based on industry-recognized credentials. The training required for these credentials will certify that individuals possess the basic skills identified by manufacturers as necessary for a career in manufacturing.
These skill certifications can and should become part of a traditional education system. Manufacturers will develop outreach programs to ensure that secondary students, parents, and guidance counselors see modern manufacturing as safe, sleek, and technology-driven.
The toolkit takes advantage of NAM’s social media message that manufacturing equals opportunity. Our #WeAreMFG campaign uses the power of video and social media to introduce young people to the new face of manufacturing: a career path that is high-tech, high-paying, and full of exciting opportunities — pointing out that manufacturing workers earn, on average, more than $77,000 in salary and benefits each year, compared with a national average of around $60,000 for workers in all industries.
The productivity, talent, and innovation of the men and women who make up the manufacturing workforce have fueled the American economy for decades. Our workforce has been, and should remain, our competitive advantage. The future is bright, but only if we have workers capable of producing leading-edge products.
The skills gap cannot be bridged overnight. And solving this challenge cannot be handed off to government or educational institutions. We also can’t launch a solution and put it on automatic pilot. The long-term success of U.S. manufacturing will depend on broad, systemic change and ongoing commitment from the manufacturing community. It will require time, effort, and resources, but if we work together to tackle the problem head on, success will be our eventual outcome.